10th April 2024
Unlocking the potential of remote telemetry solutions in oil and gas pipelines
The oil and gas industry faces demands to adopt more sustainable practices. But, given that fossil fuels will remain essential to global growth for the next 10-20 years, can the industry ever be truly sustainable and reduce its carbon dioxide (CO2), methane (CH4) and other greenhouse gas emissions? Investments in new and sustainable technologies hold the answer to this question. Here, Etienne Clauw, Associate Product Line Manager – RTUs at Ovarro, explains how remote telemetry solutions could help oil and gas operators greatly improve their sustainability measures.
Sustainability initiatives in the oil and gas industry include the 'Global Decarbonization Alliance', a group of oil and gas companies — including Siemens Energy, Tata Steel, Enel Green Power and others — with a goal to achieve net-zero scope one and two emissions by 2050. The industry is also seeing an increase in interest in alternative energy sources, such as the use of hydrogen, which has the potential to be more sustainable compared to traditional fossil fuels like coal, oil and natural gas. 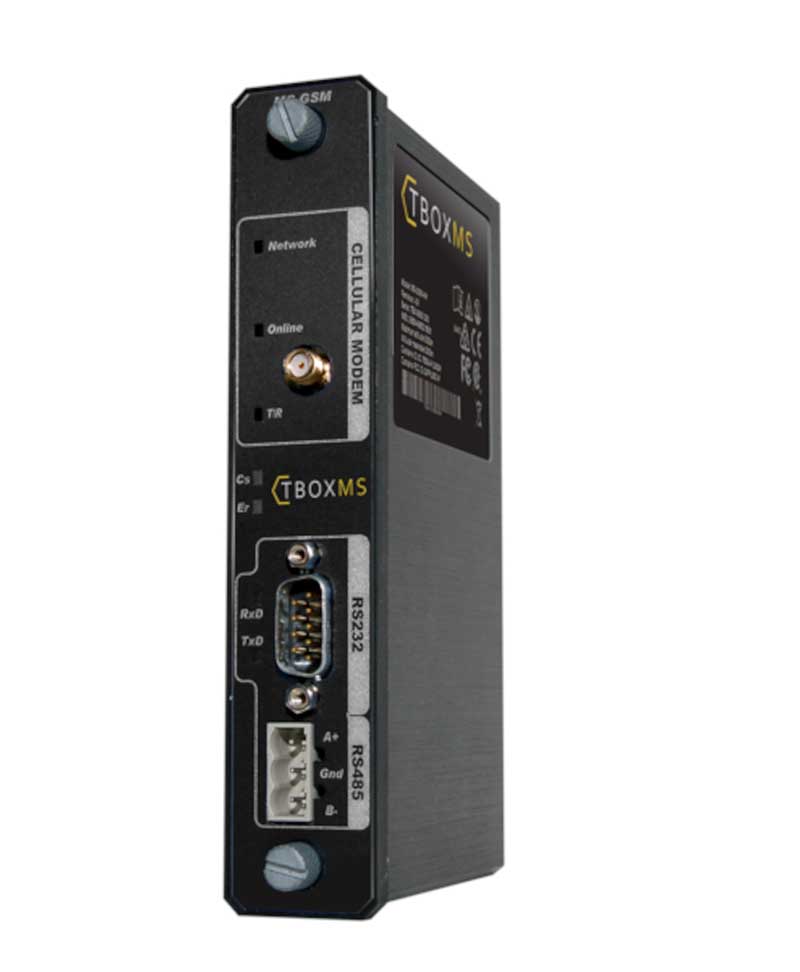
Alongside these broader initiatives, the oil and gas industry is making better use of sustainable technologies. A report by the World Future Energy Summit highlights eight ways in which, with cleantech innovations, oil and gas companies are striving to minimise costs and reduce their carbon footprint across operations. Key initiatives include the better use of data analytics to optimise production, decrease freshwater use, improve water recycling efforts and reduce methane leaks. Additionally, companies are exploring used oil recycling, streamlining processes, creating digital oilfields — similar to digital twins — for real-time monitoring and analysis and investing in renewable energy sources. All of these efforts signal a shift towards sustainability in the oil and gas sector.
Nevertheless, the use of cleantech innovations also presents operational challenges. First, there may be significant upfront costs for the technology itself. Second, challenges might relate to the complexities of integrating and maintaining these advanced solutions, including infrastructural developments or the logistical hurdles of applying the technologies in remote or offshore locations.
Third, it is necessary to comply with evolving environmental regulations. Lastly, the workforce must be trained in using the new systems. Oil and gas companies must navigate these obstacles while driving the industry towards a more sustainable future — but how?
Safe areas
One solution lies in the increased use of data and artificial intelligence (AI) for the monitoring and control of crucial assets. After all, oil and gas are among the highest value assets passed through a pipe or transported via land and sea. The main goal of remote control and monitoring is to improve efficiency in oil and gas operations, which is essential for reducing emissions.
Safety is another consideration due to the hazardous nature of the sector. Specific areas within oil and gas facilities are designated as "safe areas" or "non-hazardous areas" where the risk of fire or explosion is minimised. These safe areas typically house communications equipment such as control systems, instrumentation and networking infrastructure.
However, changes in design philosophies — including the “keep it simple” ethos — and cost-saving measures have led to the removal of safe areas from many locations. For operators, this makes it more difficult and expensive to install control and communications equipment and the power systems to operate them. Furthermore, remote locations often have little to no power and rely on solar panels or small production powered gensets.
How can oil and gas network operators improve monitoring and control of crucial assets, while also overcoming these challenges? Fortunately, remote telemetry solutions have emerged as a pivotal tool.
Ovarro’s remote telemetry units (RTUs) are equipped with cellular wireless connectivity and are designed to empower operators with real-time insights and control over their assets.
By excluding wired components and opting for compact, lower power designs with smart communication protocols, companies can not only lower installation costs but also minimise the footprint of control systems. Integrating RTUs in series or parallel with control equipment allows remote access without the need for additional modems, streamlining installation processes and reducing expenses. The added flexibility also helps overcome the absence of safe areas.
Industry players leveraging remote telemetry solutions include Beijing City Gas Group, PetroChina and Distrigas. With over 100,000 telemetry, automation and remote monitoring solutions deployed worldwide, including in critical oil and gas applications, the impact of these technologies is growing.
Remote monitoring
In one case, PetroChina Pipeline Company Limited, a subsidiary of PetroChina Limited, undertook the ambitious project of constructing over 800 kilometres of pipeline within 180 days, setting a new record in a challenging high-latitude and extremely cold environment. Facing extreme temperatures ranging from -52.3 degrees Celsius in winter to 39.8 degrees Celsius in summer, the project required robust control systems.
Implemented by Ovarro’s partner ZKCiT, a systems integrator, 22 TBox-MS Modular RTUs facilitated pipeline monitoring and control, operating reliably despite temperatures as low as -43 degrees Celsius. Crucially, the remote telemetry systems exceeded the customers’ specified operational limits and ensured continuous operation of the pipeline.
This example shows how wireless communication technologies, leveraging specialised devices like RTUs, can enhance the monitoring and control of crucial assets. The result is more efficient, sustainable oil and gas operations.
Ovarro also features in Berg Insight’s new market report, IIoT Applications in the Oil and Gas Industry – 5th Edition, about the latest developments in the use of wireless technologies in the oil and gas industry.